8# Garnet Abrasive Sand Sandblasting Medias 2mm-2.36mm No Scratch
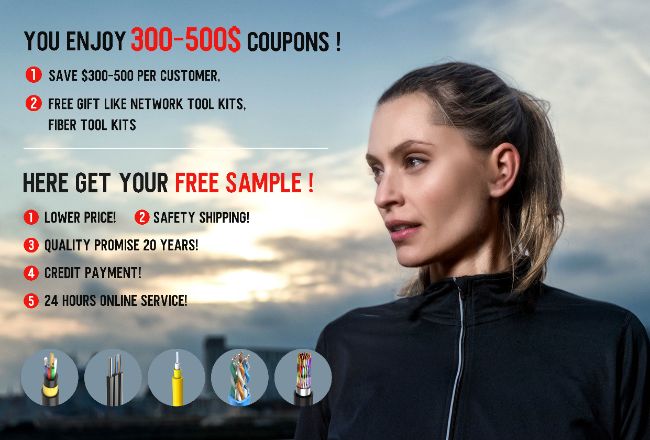
Contact me for free samples and coupons.
Whatsapp:0086 18588475571
Wechat: 0086 18588475571
Skype: sales10@aixton.com
If you have any concern, we provide 24-hour online help.
xName | Garnet Media For Sandblasting | Mohs Hardness | 7.1 |
---|---|---|---|
True Density | 3.8g/cm³ | Brand Name | Huitai |
Certification | ISO9001 | Grain Size | 2-2.36mm |
Place Of Origin | China | ||
Highlight | 8# Garnet Abrasive Sand,Garnet Abrasive Sand 2mm,Abrasive Garnet Sand No Scratch |
Huitai 8# Garnet Abrasive Sand Sandblasting Medias
1. Product Introduction
Garnet sand, ground from garnet as raw material, has the characteristics of high hardness, high temperature resistance, stable chemical properties, uniform particles, high grinding efficiency and no scratch. It is suitable for various metal, non-metal, plastic and other material device surface sandblasting treatment industry.
Chemical analysis | SiO2 | Al2O3 | FeO | CaO | MgO2 |
Wt% | 36-40 | 20-24 | 22-24 | 6-9 | 8-13 |
Common particle size(Can be customized according to customer requirements)
8# | 16# | 30# | 40# | 60# |
2-2.36mm | 1-1.18mm | 500-600μm | 355-425μm | 212-350μm |
80# | 100# | 120# | 150# | 180# |
150-180μm | 106-125μm | 90-106μm | 63-75μm | 45-63μm |
2. Characteristics
① The texture of garnet sand is hard, with a Mohs hardness of more than 7.1, which is higher than that of commonly used quartz sand, sea sand, river sand and other sandblasting materials, and has a long service life.
② Because garnet is a crystal of an isometric system and has no cleavage, which it is easy to form approximate cube particles with edges and angles after making it into sandblasting, and the effect of sandblasting and rust removal is better. It can not only completely remove the rust, oxide skin, coating and its pollutants on the metal surface, but also because of its high hardness, it can produce an ideal angular rough surface on the cleaned metal surface, increasing the surface area of the metal, improving the adhesion of the interface, and making the binding force of corrosion-resistant protective coating and the metal surface significant. So it can enhance to improve the bonding performance of the coating and the metal surface.
③ The density of garnet sand is larger, usually about 4g/cm³, strong impact force, which can better clean the metal surface.
④ High strength. Treating the metal surface,garnet sand is not easy to break. Even after it is broken, it will produce new angular, almost cubic particles, so that it can be used repeatedly, usually up to 20 times. It is 20 times of siliceous sand (sea sand or river sand) and more than 2 times of quartz sand (artificial), and its relative cost is low once used.
3. Application
① Surface pretreatment of metal and steel structures, etc
This is one of the more widely used fields of garnet sandblasting. It can be used for electroplating, spray painting, spraying and other all covered before sandblasting processing, which can achieve a clean surface, and improve the roughness of the substrate surface, enhance the adhesion of the coating, extend the life of the coating, especially for ships and other large equipment.
② Surface cleaning of workpiece
It is mainly used to remove dirt and impurities on the surface of objects, such as casting parts, stamping parts, welding parts, heat treatment parts and other metal work pieces and oxide skin, residue, dirt; Cleaning surface of non-metallic products, removing the black spots on the surface of ceramic embryo.
③ Processing glitch
Machined parts tiny burr removal, injection parts overflow glue burr elimination. It can be said to be a correction to make the surface flatness of the workpiece better light finishing process.
④ Refurbishment of old workpieces
For the refurbishment and cleaning of all moving parts such as automobiles, motorcycles, electromechanical equipment, etc., garnet sand can also be used, which can not only restore the metallic luster of the workpiece, but also have no problem of sand inlaying. At the same time, it can also eliminate the fatigue stress of workpieces and extend their service life.