High Strength Garnet Abrasive Sand Self Dispersion For Sandblasting Industry
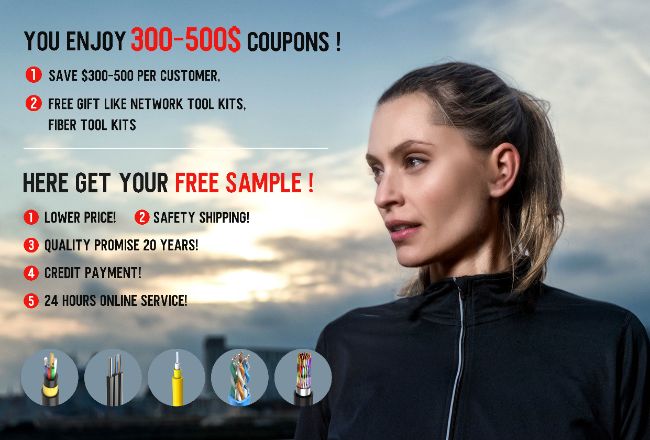
Contact me for free samples and coupons.
Whatsapp:0086 18588475571
Wechat: 0086 18588475571
Skype: sales10@aixton.com
If you have any concern, we provide 24-hour online help.
xName | Mesh Garnet Abrasive | Place Of Origin | China |
---|---|---|---|
Mohs Hardness | 7.1 | Density | 4g/cm³ |
Melting Point | 1340 ℃ | Color | Brownish Red |
Certification | ISO9001 | ||
Highlight | High Strength Garnet Abrasive Sand,Garnet Abrasive Sand Self Dispersion,Garnet Sandblasting Sand |
Huitai Garnet Abrasive Sand In The Machinery Sandblasting Industry
1. Product Introduction
Garnet sand, ground from garnet as raw material, is characterized by high hardness, high temperature resistance, stable chemical properties, uniform particles and high grinding efficiency. It is suitable for waterjet cutting industry; various metal, non-metal, plastic and other material device surface sandblasting treatment industry; ultra-precise grinding in machinery industry, precision casting; grinding of CRT glass case, optical glass, silicon wafer, etc.
Chemical analysis | SiO2 | Al2O3 | FeO | CaO | MgO2 |
Wt% | 36-40 | 20-24 | 22-24 | 6-9 | 8-13 |
Morphology: | Prismatic, Irregular | Crystal shape: | Equiaxed crystal system |
Color: | Brownish red | Melting point: | 1340 ℃ |
Mohs hardness: | 7.1 | Density: | 4g/cm³ |
Number of cycles: | 20 times or more | Water absorption: | Non-absorbent |
Magnetic: | Weakly magnetic | Transparency: | Transparent |
Dispersion: | Self-dispersion | Homogeneity: | Homogeneous body |
Harmful free silicon content: None |
Deconstruction: Irregular deconstruction surface |
2. Characteristics
Good polishing effect: After polishing, garnet sand has high surface finish, which can be used for high-end products such as jewelry.
Good corrosion resistance: it is not easy to be chemically corroded by acid and alkali, suitable for use in harsh environment.
Good thermal stability: can withstand high temperature environment, with a melting point of about 1713℃.
Outstanding optical properties: it can produce beautiful color clashing effect and patterns with different color shades.
3. Application
① Surface pretreatment of metal and steel structures, etc
This is one of the more widely used fields of garnet sandblasting. It can be used for electroplating, spray painting, spraying and other all covered before sandblasting processing, which can achieve a clean surface, and improve the roughness of the substrate surface, enhance the adhesion of the coating, extend the life of the coating, especially for ships and other large equipment.
② Surface cleaning of workpiece
It is mainly used to remove dirt and impurities on the surface of objects, such as casting parts, stamping parts, welding parts, heat treatment parts and other metal work pieces and oxide skin, residue, dirt; Cleaning surface of non-metallic products, removing the black spots on the surface of ceramic embryo.
③ Workpiece burr treatment
Machined parts tiny burr removal, injection parts overflow glue burr elimination. It can be said to be a correction to make the surface flatness of the workpiece better light finishing process.
④ Etching non-slip
Metal products, non-metal products surface etched patterns, characters and anti-slip treatment, such as: marble, anti-slip handle, seal, stone inscription and so on.
⑤ Clothing whiskering treatment
This is mainly used in the jeans industry. For the frosting, whitening and whiskering effects of the jeans industry, they can be achieved in this way. However, the garnet sand used in this process is generally relatively fine.
⑥ Refurbishment of old workpieces
For the refurbishment and cleaning of all moving parts such as automobiles, motorcycles, electromechanical equipment, etc., garnet sand can also be used, which can not only restore the metallic luster of the workpiece, but also have no problem of sand inlaying. At the same time, it can also eliminate the fatigue stress of workpieces and extend their service life.
⑦ Matte effect of various materials, polishing
This can be used to eliminate surface traces of all metal and non-metallic products (plastic, crystal, glass, etc.) and matte fog surface treatment to improve the surface grade of the product. In particular, the fog effect on the mold surface can not only improve the accuracy of the mold, but also will not damage the mold surface.