High Durability Spin Faster Non-porous and durable Ceramic Shot Peening
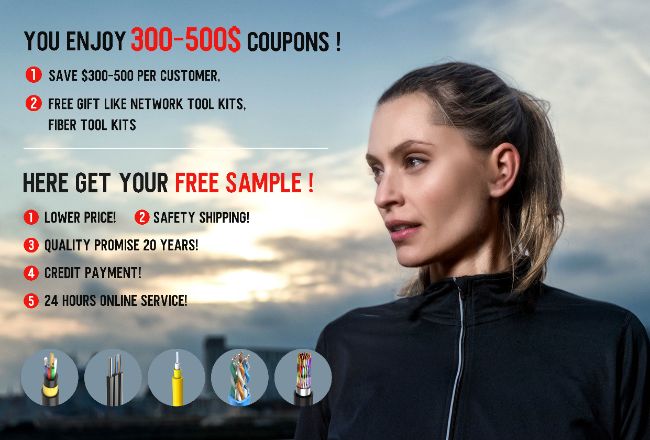
Contact me for free samples and coupons.
Whatsapp:0086 18588475571
Wechat: 0086 18588475571
Skype: sales10@aixton.com
If you have any concern, we provide 24-hour online help.
xCorrosion Resistance | High | Melting Point | 2040 °C (3700 °F) |
---|---|---|---|
Applications | Valves And Bearings | Hardness According To Vickers | < 1500 (HV10) |
Material | Aluminum Oxide | Environmental Impact | Low |
Highlight | Corrosion Resistant Ceramic Shot Peening,Bearings Ceramic Milling Media,Aluminum Oxide Shot Peening Media |
Product Description:
Zirconia grinding medium ball is a type of ceramic ball with a ZrO2 content of over 90%, achieved by adding a stabilizer. Compared to Al2O3 ceramic balls, these balls exhibit higher grinding efficiency and wear resistance. They also have a smoother and harder surface, avoiding any contamination during use. With excellent roundness and a reasonable size distribution, they have high hardness, high strength, and high toughness, as well as excellent wear and corrosion resistance. This makes them highly efficient and cost-effective for industrial use in various industries such as ceramics, building materials, chemicals, coatings, electronics, machinery, food, medicine, and cosmetics.
Zirconia is a metal oxide that can be produced by reacting zirconium silicate or other compounds containing zirconium. The main component of zirconia is zirconium, which is obtained from zircon sand. Australia, Indonesia, South Africa, Vietnam, and coastal areas of the South China Sea are the top producers of zircon sand. Australia and Indonesia are known for producing high-quality zircon sand with the right chemical composition and desirable whiteness, although it may come at a higher cost.
Zirconium silicate beads are the result of continuous process optimization and upgrading of molding and grinding technology. These beads are made by a high-temperature sintering process, resulting in dense, pore-free, and spherical-shaped structures. They have a medium hardness and density, making them suitable for medium and low viscosity slurry dispersion and grinding. Furthermore, their small particle size makes them ideal for material polishing and spraying.
Features:
1. Zirconium beads, with a zirconia content of 94-95%, have high wear-resistance and are more durable than other grinding media. They also have good fluidity, roundness, and a smooth surface, making them suitable for applications with lower equipment wear resistance requirements.
2. TZP zirconia beads contain approximately 95% zirconium and 4.8% yttrium, making them 1.6 times denser than regular zirconia beads. This results in higher grinding efficiency under the same conditions.
3. These beads have excellent impact resistance and low wear rates. Their toughness allows them to withstand high speeds and concentrations in machinery without cracking or peeling, and they experience only half the wear of zirconia silicate beads. Their low wear also helps prevent material contamination.
4. The roundness and smooth surface of TZP zirconia ceramic beads contribute to their ability to minimize equipment wear.
5. These beads offer high grinding efficiency and have a longer service life, resulting in lower overall operational costs.
6. They are especially suitable for high viscosity, wet grinding, and dispersion processes.
7. Additionally, these beads have high mechanical strength, impact resistance, and a good crystal density and toughness, preventing the occurrence of broken balls.
Applications:
Zirconia balls are predominantly utilized for grinding applications, but can also serve as effective tools for polishing and sand blasting.
Ceramic powder, coatings, and other substances can be crushed and dispersed utilizing zirconia balls. This versatile material can also assist in the production of electronic components such as ceramic capacitors, pigments, inks, and insulation materials. In addition, zirconia balls are commonly employed in precision ceramic crushing for the processing of electronic powders, materials used in PTC, LED phosphors, electronic pastes, magnets, fluorescent powders, medicines, piezoelectric ceramics, cathodes for lithium batteries, and NTC thermistors, as well as in the production of capacitors.
Furthermore, zirconia balls are incredibly useful for grinding high hardness materials like alumina, aluminum, glass, quartz, feldspar, glaze, and others. These balls are known for their exceptional toughness and can be effectively used in abrasive mills, stirring mills, and other high-speed equipment. They are often utilized in the grinding of materials for paint, graphite coatings, and food and drug-grade substances.
In addition to its application as grinding media, zirconia balls can also serve as highly effective wear-resistant coatings, with commonly used sizes ranging from 0.5 to 3mm. With its high temperature resistance, zirconia balls can also be utilized in kilns.
For more precise applications, zirconia balls can be finely machined into wear-resistant ceramic balls for use in ceramic bearings and valves. However, in terms of precision, alumina is often preferred over zirconia for these purposes.
Customization:
Brand Name: Fine-tech
Model Number: 0.8mm
Place of Origin: Changshan China
Corrosion Resistance: High
Hardness according to Vickers: < 1500 (HV10)
Durability: High
Melting Point: 2040 °C (3700 °F)
Applications: Valves And Bearings
Customized Service for Fine-tech Ceramic Shot Peening
Our Ceramic Shot Peening product offers strong corrosion resistance, making it ideal for use in harsh environments. Its high durability ensures long-lasting performance, and its hardness according to Vickers is less than 1500 (HV10), providing excellent dimensional stability.
With a melting point of 2040 °C (3700 °F), our Ceramic Shot Peening is able to withstand high temperatures, making it suitable for various industrial applications. Our product is manufactured in Changshan, China, ensuring high quality and reliability.
At Fine-tech, we understand that every customer's needs are unique. That's why we offer customized services to meet your specific requirements. Our team of experts will work closely with you to provide tailored solutions for your project, ensuring optimal results and maximum satisfaction.
Packing and Shipping:
Our Ceramic Shot Peening product is carefully packaged and shipped to ensure its safe arrival to our customers.
Each batch of Ceramic Shot Peening is packaged in high-quality, durable containers that are designed to withstand the rigors of shipping and handling. The containers are sealed to prevent any leakage or damage during transport.
Inside the container, the Ceramic Shot Peening is securely packed in protective material to prevent any shifts or movement during shipping. This ensures that the product arrives at its destination in the same condition as when it left our facility.
Our Ceramic Shot Peening is shipped using trusted and reliable shipping carriers, such as FedEx, UPS, or DHL. We also offer the option for customers to arrange their own shipping if they have a preferred carrier.
We take great care in packaging and labeling our shipments to ensure that they are handled properly and reach their destination on time. Our team closely monitors the shipment and provides tracking information to our customers so they can track their order's progress.
For international shipments, we comply with all necessary customs regulations and provide all required documentation to ensure a smooth and timely delivery.
At Ceramic Shot Peening, we strive to provide the best packaging and shipping experience for our customers. If you have any concerns or special requests, please don't hesitate to contact us.
FAQ:
- Q: What is the brand name of this product?
A: The brand name is Fine-tech. - Q: What is the model number of this product?
A: The model number is 0.8mm. - Q: Where is this product manufactured?
A: This product is manufactured in Changshan, China. - Q: What is the size of the ceramic shot used in this product?
A: The size of the ceramic shot used is 0.8mm. - Q: How does ceramic shot peening improve the surface of a material?
A: Ceramic shot peening creates compressive stresses on the surface of a material, which can improve its fatigue resistance and strength.