High Tensile Strength Component Nearly Frictionless Ceramic Shot Peening
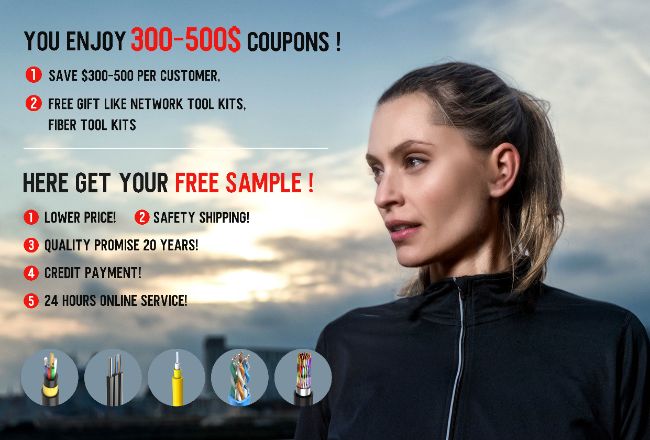
Contact me for free samples and coupons.
Whatsapp:0086 18588475571
Wechat: 0086 18588475571
Skype: sales10@aixton.com
If you have any concern, we provide 24-hour online help.
xApplications | Valves And Bearings | Material | Aluminum Oxide |
---|---|---|---|
Environmental Impact | Low | Durability | High |
Melting Point | 2040 °C (3700 °F) | Tensile Strength | High |
Highlight | Corrosion Resistant Ceramic Shot Peening,1.0mm Ceramic Shot Peening |
Product Description:
Zirconia (ZrO2) microbeads possess numerous advantages that make them highly desirable in the field of grinding. These include high strength, high toughness, high density, high hardness, excellent wear resistance, and corrosion resistance. These qualities make zirconia microbeads ideal for industrial applications. With their impressive combination of density, particle size uniformity, sphericity, strength, hardness, toughness, and corrosion resistance, these microbeads exhibit wear resistance up to 5-10 times that of ordinary glass. Additionally, their ease of production and ability to be cleaned and reused make them a highly efficient option for various industrial processes.
High-performance zirconia microbeads typically have a particle size ranging between 0.8mm-2.2mm and a zirconia content of 94.6%. These microbeads are characterized by their white luster, Mohs hardness of more than 9 (HRA can reach more than 90), and density exceeding 6.0g/cm3. With their high toughness, wear resistance, thermal expansion coefficient of 4-7×10-6/℃, and compressive strength of 1000-1300MPa, zirconia microbeads are able to maintain low wear rates (0.02kg/h).
Zirconium silicate beads are the result of process optimization and continuous upgrades in molding and grinding technology. They are created through a high temperature sintering process, resulting in beads with no pores, a dense crystal phase, and a spherical shape. These beads are medium-hardness and exhibit a good wear resistance, making them ideal for dispersing and grinding low to medium viscosity slurries. Additionally, zirconium silicate beads with smaller particle sizes can be used for polishing materials through spraying techniques.
Features:
Zirconium beads with a zirconia content of 94-95% are known for their high zirconium content, making them resistant to wear and highly durable. They have excellent fluidity and a spherical shape, with a smooth surface that meets the requirements for low equipment wear compared to other grinding media.
TZP zirconia beads, which contain approximately 95% zirconium and 4.8% yttrium, have a specific gravity 1.6 times higher than regular zirconia beads, resulting in higher grinding efficiency under the same conditions.
These beads are also known for their impact resistance and low wear. They are tough, do not crack or peel at high speeds and concentrations, and have only 1/2 the wear rate of zirconia silicate beads, ensuring minimal material contamination.
With excellent roundness and a smooth surface, TZP zirconia ceramic microbeads contribute to lower equipment wear for efficient grinding processes. They not only have high grinding efficiency, but also boast a long service life and low overall operating costs.
These beads are particularly suitable for high viscosity, wet grinding and dispersion processes, and are characterized by their high mechanical strength, impact resistance, and good crystal density and toughness. They do not experience any ball breakage, ensuring consistent and reliable performance.
Applications:
Zirconia balls are primarily utilized for grinding purposes, but they can also be effectively employed for sand blasting and polishing. These balls are suitable for crushing and dispersing ceramic powders, coatings, and other materials, making them ideal for a variety of applications including ceramic capacitors, pigments, ink, food processing, insulation materials, electronic powders, and more. They are also utilized in the processing of precise ceramics, electronic materials, PTC, LED phosphors, electronic pastes, magnetic materials, fluorescent powders, medicines, piezoelectric ceramics, lithium battery cathode materials, NTC thermistors, as well as capacitors.
Aside from grinding, zirconia balls are also suitable for use as grinding media for materials with high hardness such as alumina, aluminum, glass, quartz, feldspar, and glaze. These balls are known for their high toughness, making them suitable for use in high-speed equipment such as abrasive mills and stirring mills. They are commonly used in the grinding of paint, graphite coatings, and food-grade raw materials.
With its high wear resistance, zirconia balls can also be used as wear-resistant coatings, along with rubber. The most commonly used sizes for wear-resistant ceramic balls are 0.5, 1, 2, and 3mm.
The high temperature resistance of zirconia balls also makes them suitable as kiln balls, with alumina wear-resistant ceramic balls able to withstand temperatures of over 1000 degrees. These balls can also be finely machined into precision wear-resistant ceramic balls for use in ceramic bearings and valves. They are also effective as grinding media for non-metallic minerals such as calcium carbonate.
Lastly, zirconia balls can also be used for polishing, sandblasting, and other surface treatment applications due to their high hardness and wear resistance, making them a versatile and valuable material in various industries.
Customization:
Brand Name: Fine-tech
Model Number: 3.0mm
Place of Origin: Changshan, China
Environmental Impact: Low
Applications: Valves And Bearings
Abrasion Resistance: High
Corrosion Resistance: High
Durability: High
At Fine-tech, we provide top-of-the-line customized solutions for your ceramic shot peening needs. Our product is designed to have a strong corrosion resistance, ensuring long-lasting and reliable performance. The dimensional stability of our ceramic shot peening guarantees precise and accurate results, making it the ideal choice for critical applications.
Our product is specifically designed for valves and bearings, offering high abrasion resistance and durability. It is perfect for applications where wear and tear are a concern, providing a cost-effective solution for maintaining equipment.
In addition to its high performance, Fine-tech's ceramic shot peening also has a low environmental impact, making it an eco-friendly choice for your business. Our team in Changshan, China, utilizes advanced technology and strict quality control measures to ensure the highest quality product for our customers.
Choose Fine-tech for abrasion-resistant linings and customized solutions that meet your specific needs. Contact us today to learn more about our ceramic shot peening and how we can help improve your production process.
Packing and Shipping:
Our Ceramic Shot Peening product will be carefully packaged and shipped to ensure its safe arrival to our valued customers. We take great care in our packaging process to avoid any damage during transit.
- The Ceramic Shot Peening product will be packed in sturdy boxes to protect it from external damage.
- Each box will contain the appropriate amount of Ceramic Shot Peening product to ensure secure packaging and to minimize the risk of breakage.
- All boxes will be labeled with the product name, quantity, and any necessary handling instructions.
We offer various shipping methods to accommodate our customers' needs:
- Standard Shipping: Our default shipping method is Standard Shipping, which typically takes 3-5 business days for delivery.
- Expedited Shipping: Customers can choose Expedited Shipping for faster delivery, which typically takes 1-3 business days.
- International Shipping: We also offer international shipping options for our customers outside of the United States.
For large orders, we may use a freight carrier to ensure safe and efficient delivery.
Once your order has been shipped, we will provide you with a tracking number so you can monitor the status of your shipment.
Thank you for choosing our Ceramic Shot Peening product. We are committed to providing you with a high-quality product and ensuring its safe delivery.
FAQ:
- Q: What is Ceramic Shot Peening?
A: Ceramic Shot Peening is a surface treatment process in which small ceramic particles are shot at a material to improve its surface properties. - Q: What is the brand name of this product?
A: The brand name of this product is Fine-tech. - Q: What is the model number of Ceramic Shot Peening?
A: The model number of Ceramic Shot Peening is 3.0mm. - Q: Where is this product manufactured?
A: This product is manufactured in Changshan, China. - Q: What are the benefits of using Ceramic Shot Peening?
A: Ceramic Shot Peening can improve surface hardness, fatigue strength, and resistance to corrosion and wear.