1.0mm Alumina Ceramic Grinding Balls 9 Mohs High Griding Effenicy
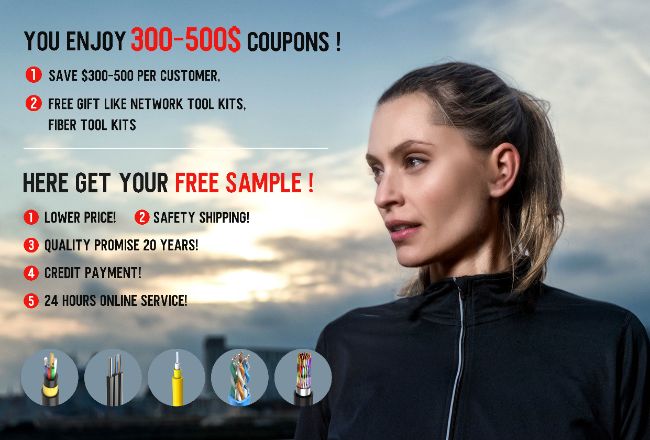
Contact me for free samples and coupons.
Whatsapp:0086 18588475571
Wechat: 0086 18588475571
Skype: sales10@aixton.com
If you have any concern, we provide 24-hour online help.
xMaterial | Zirconia | Shape | Grit |
---|---|---|---|
Chemical Composition | ZrO2 | Usage | Polishing , Industry |
Application | Steel , Surface Treatment | Mohs Hardness | 9 |
Highlight | 1.0mm Alumina Ceramic Grinding Balls,Alumina Ceramic Grinding Balls 9 Mohs |
1.0mm High Griding Effenicy Zirconia Shot Peening Media Pellet
DESCRIPTION
Zirconia itself is a metal oxide that can be made by reacting zirconium silicate or prepared from other compounds containing zirconium, the main component of which is zirconium. The raw material for zirconium is zircon sand, which is mainly produced in Australia, Indonesia, South Africa, Vietnam and the coastal areas of the South China Sea. Among them, Australia and Indonesia's zirconium sand is the best, not only the chemical composition meets the requirements, the production of zirconium silicate whiteness is also very good, of course, its price is relatively high.
ATTRIBUTE
The particle size of high-performance zirconia microbeads is between 0.8mm-2.2mm, with 94.6% zirconia content, white luster, Mohs hardness of more than 9 (HRA can reach more than 90), density of more than 6.0g/cm3. Due to high toughness and wear resistance, thermal expansion coefficient of 4-7×10-6/℃, compressive strength of 1000-1300MPa, with low wear (0.02kg/h).
APPLICATION
A. According to its wear resistance, in addition to rubber, can also be used as wear-resistant coatings, commonly used wear-resistant ceramic ball models are 0.5, 1, 2, 3mm.
B. Can be used as the ball of kiln because of its high temperature resistance. Alumina wear-resistant ceramic ball can withstand the high temperature of more than 1000 degrees.
C. Fine machined into precision wear resistant ceramic balls for ceramic bearings and ceramic valves.
ADVANTAGES
1. High strength and wear resistance. The main component of ceramic shot is zirconia, which is characterized by small crystal size and high wear resistance.
2. Ceramic shot has high hardness, with Vickers hardness (microhardness) of 700HV and Rockwell hardness of 600HRC The density and specific gravity are also much higher than those of glass beads.
3. No dust, high abrasion resistance and strength make it difficult for ceramic shot to be broken during sand blasting, so it is not easy to generate dust.
4. Sandblasting effect: the surface finish is high. Using ceramic shot sandblasting can achieve smooth satin surface brightness. Using ceramic shot of the same specification is 60-70% lower than that of glass bead sandblasting.