850μM-1180μM Ceramic Bead Blasting Material Durable Shot Peening
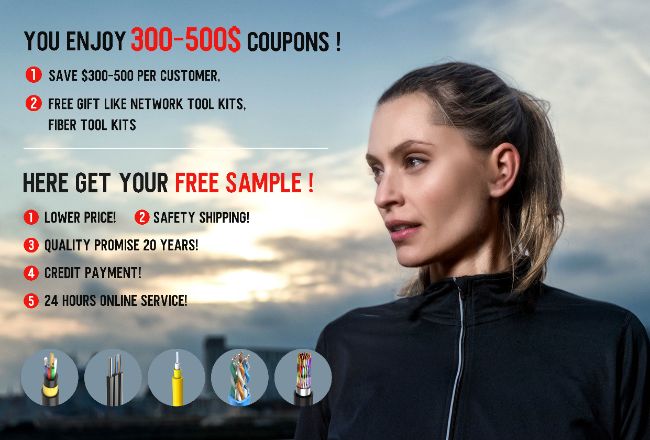
Contact me for free samples and coupons.
Whatsapp:0086 18588475571
Wechat: 0086 18588475571
Skype: sales10@aixton.com
If you have any concern, we provide 24-hour online help.
xName | Ceramic Bead Blasting Media | Zro2 | 65% |
---|---|---|---|
Size | 850-1180μm | Usage | Grinding,Sandblasting |
Color | White | Material | ZrO2 |
Application | Abrasive Refractory Industry | ||
Highlight | 850μm Ceramic Bead Blasting,1180μm Ceramic Bead Blasting,Ceramic Bead Blasting Material |
Ceramic Bead Blasting Media 850-1180μm Durable Shot Peening
APPLICATION
Ceramic beads can be used for blast pretreatment beforecoating or plating.
Among all surface cleaning methods, the ceramic beads sandblasting method is a thorough, universal, and extensive method, because:
1. Sandblasting is more efficient, thorough and cheaper than other pretreatment processes.
2. The sandblasting process allows you to freely choose the cleanliness and roughness of your workpiece.
QUALITY
1. High strength and wear resistance. The main component of ceramic shot is zirconia, which is characterized by small crystal size and high wear resistance.
2. Ceramic shot has high hardness, with Vickers hardness (microhardness) of 700HV and Rockwell hardness of 600HRC The density and specific gravity are also much higher than those of glass beads.
3. No dust, high abrasion resistance and strength make it difficult for ceramic shot to be broken during sand blasting, so it is not easy to generate dust.
4. Sandblasting effect: the surface finish is high. Using ceramic shot sandblasting can achieve smooth satin surface brightness. Using ceramic shot of the same specification is 60-70% lower than that of glass bead sandblasting.
5. It is applicable to various metals and nonmetals, such as titanium alloy, magnesium alloy, aluminum alloy, stainless steel, carbon steel, brass and alloy, acrylic, plastic and other materials. Ceramic shot will not react or oxidize with metal, and there is no metal residue, so it will not affect the color of the workpiece.
PERFORMANCE PARAMETER
1 | Vickers hardness | 643~785HV |
2 | Dust Pollution | NO |
3 | Metal contamination | NO |
4 | Cycle index | many times |
5 | Service life | long |
6 | Equipment wear | low |