Z850 Low Dust Blasting Media 150μm-212μm Ceramic Microspheres Spherical
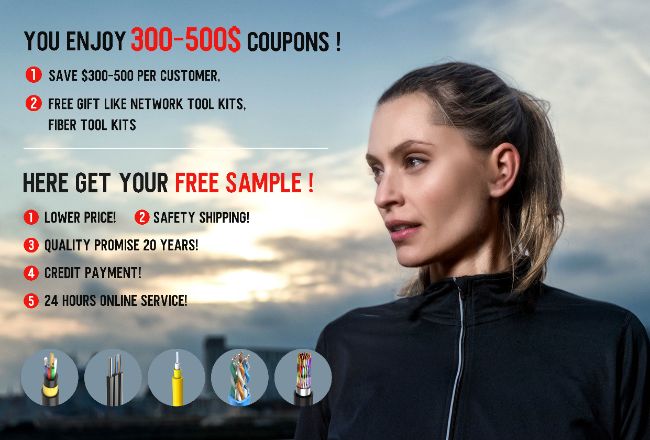
Contact me for free samples and coupons.
Whatsapp:0086 18588475571
Wechat: 0086 18588475571
Skype: sales10@aixton.com
If you have any concern, we provide 24-hour online help.
xName | Ceramic Microbeads | Size | 850-1180μm |
---|---|---|---|
Metal Contamination | No | Shape | Spherical |
Color | White | Application | Abrasive Refractory Industry,Polishing |
Chemical Composition | SiO2,ZrO2 | ||
Highlight | Z850 Low Dust Blasting Media,Low Dust Blasting Media 150μm,212μm Ceramic Microspheres |
Ceramic Low Dust Bead Blasting 150-212μm Durable Microsphere
CERAMIC BEAD BLASTING DESCRIPTION
The main component of ceramic beads is zirconia, which is mainly used for surface treatmentsuch as sand blasting and shot peening. The production process of ceramic shot is to melthigh-quality imported zircon sand into liquid at high temperature, and then spray it into balls.The zirconia ceramic spheres are sieved and removed by magnetic separation to obtain particles with high roundness, high strength and uniform particle size. The spherical particles of ceramic shot can achieve better surface brightness during sandblasting, while the workpiece itself does not change color. It is widely used for sandblasting and surface treatment of aviation parts, stainless steel plates, structural parts, stainless steel kitchenware, medical devices, mobile phone / laptop shell, automobile chassis / engine, sports equipment and other industries.
CERAMIC BEAD BLASTING Performance Parameter
No. | Parameter | Value |
1 | Color | White |
2 | Shape | sphere/Bead/Ball |
3 | Production technology | melting method |
4 | Chemical composition | ZrO2 65% SiO2 35% |
5 | Density | 3.86g/cm3 |
6 | Vickers hardness | 643~785HV |
7 | Dust Pollution | NO |
8 | Metal contamination | NO |
9 | Cycle index | many times |
10 | Service life | long |
11 | Equipment wear | low |
CERAMIC BEAD BLASTING FEATURES
White color, high sphericity and smooth surface beads.
Utilization rate(20 – 30 times) higher than glass blasting media.
High hardness, unbreakable, can be recycled and used repeatedly, long service life, reduce energy consumption and reduce costs.
Lower metal surface roughness.
Less operation pressure and reduced abrasive velocity needed than glass blasting media, thus have far less abrasive breakdown and dust generation, results in cleaner working environment and better operator visibility.
Strong mechanical resistance and high toughness, but gentle with equipment and tools preserving work parts, and no metallic contamination for treated parts.
CERAMIC BEAD BLASTING Advantages
1. High strength and wear resistance. The main component of ceramic shot is zirconia, which is characterized by small crystal size and high wear resistance.
2. Ceramic shot has high hardness, with Vickers hardness (microhardness) of 700HV and Rockwell hardness of 600HRC The density and specific gravity are also much higher than those of glass beads.
3. No dust, high abrasion resistance and strength make it difficult for ceramic shot to be broken during sand blasting, so it is not easy to generate dust.
4. Sandblasting effect: the surface finish is high. Using ceramic shot sandblasting can achieve smooth satin surface brightness. Using ceramic shot of the same specification is 60-70% lower than that of glass bead sandblasting.