White Ceramic Blasting Media with 65% ZrO2 Chemical Composition
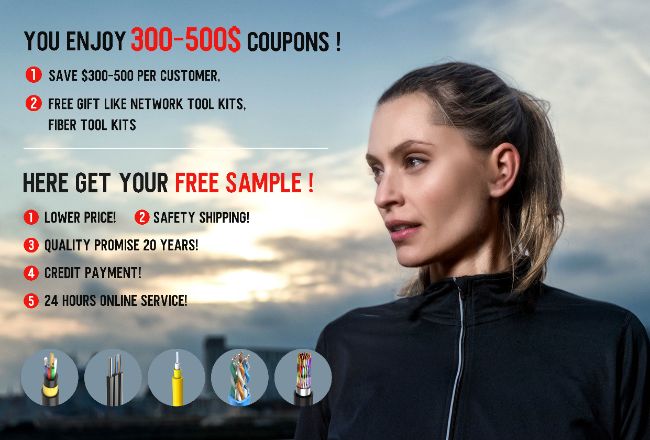
Contact me for free samples and coupons.
Whatsapp:0086 18588475571
Wechat: 0086 18588475571
Skype: sales10@aixton.com
If you have any concern, we provide 24-hour online help.
xUsage | Polishing | Service Life | Long |
---|---|---|---|
Abrasive Grain | Alumina Oxide | Melting Point | 2050°C |
Equipment Wear | Low | Material | Ceramic |
Highlight | 65% ZrO2 Ceramic Blasting Media,Polishing White Ceramic Blasting Media |
Product Description:
Ceramic beads is a Zirconia based spherical blasting media, with smooth surface and good elasticity, no iron polution, and can be recycled multi time. It performs efficiently both in dry or wet blasting equipment.
Ceramic beads also called ceramic media, ceramic bead blasting media, or ceramic blasting beads. It is of high hardness, good elasticity, high gloss and high impact strength. Ceramic blasting beads mainly used for blast cleaning, debluring, removing oxice layers of castings and forging parts, also for metal surface finishing, and pretreatment before coating and plating.
The main component of ceramic shot is zirconia, which is mainly used for surface treatment such as sand blasting and shot peening. The production process of ceramic shot is to melt high-quality imported zircon sand into liquid at high temperature, and then spray it into balls. The zirconia ceramic spheres are sieved and removed by magnetic separation to obtain particles with high roundness, high strength and uniform particle size. The spherical particles of ceramic shot can achieve better surface brightness during sandblasting, while the workpiece itself does not change color. It is widely used for sandblasting and surface treatment of aviation parts, stainless steel plates, structural parts, stainless steel kitchenware, medical devices,mobile phone / laptop shell, automobile chassis / engine, sports equipment and other industries.
Ceramic Beads blasting media are high-tech blastingmedia which are made by high quality zirconia powder as raw material, then fused in an electric furnace under high temperature over 2000 degrees, finally made into different micro beads through special technology. Its superior properties make it outlast many other abrasives, giving it both economical and performance advantages.
Features:
Surface treatment consistency
Consistency of metallic light, the blasting strength is as good as steel balls processing effect, much higher than the glass beads strength. And can achieve adequate metal depth.
Environmental Friendly
Low crushing rate, no dust, uniform particle size, high wear resistance, re-elasticity, no hidden danger of silicosis, it is harmless to the human body.
Low equipment loss
Ceramic sand has smooth surface, high sphericity, good elasticity and low wear, can protect the equipment, whether it is dry spray or wet spray.
Why Ceramic Shot is a Good Choice ?
1. High strength and wear resistance. The main component of ceramic shot is zirconia, which is characterized by small crystal size and high wear resistance.
2. Ceramic shot has high hardness, with Vickers hardness (microhardness) of 700hv and Rockwell hardness of 600hrc. The density and specific gravity are also much higher than those of glass beads.
3. No dust, high abrasion resistance and strength make it difficult for ceramic shot to be broken during sand blasting, so it is not easy to generate dust.
4.Sandblasting effect: the surface finish is high. Using ceramic shot sandblasting can achieve smooth satin surface brightness. Using ceramic shot of the same specification is 60-70% lower than that of glass bead sandblasting.
5. It is applicable to various metals and nonmetals, such as titanium alloy, magnesium alloy, aluminum alloy, stainless steel, carbon steel, brass and alloy, acrylic, plastic and other materials. Ceramic shot will not react or oxidize with metal, and there is no metal residue, so it will not affect the color of the workpiece.
6. It is suitable for dry blasting and wet blasting. The surface of ceramic shot is very smooth, and the wear of sand blasting equipment is very small.
7. Ceramic shot has high sandblasting efficiency and long service life, and its recycling times can reach 25 times of glass beads.
8. The roundness is high, and the proportion of abnormal balls and snowman balls adhered between the spheres is low.
Strong chemical resistance: Guarantees constant performance eg. consistent Surface blasting effect.
Low dust emission: Does not contaminate the work piece surface, and no hidden danger of silicosis, it is harmless to the human body.
Not easy to break: Recyclable,and can reduce the refueling times, improve working efficiency.
Suitable for both dry and wet blasting: whether it is dry spray or wet spray, ceramic shot can protect the equipment.
High hardness: 700hv of Vickers hardness (microhardness) and 600hrc of Rockwell hardness.
Technical Parameters:
Parameter | Value |
---|---|
Abrasive Grain | Alumina Oxide |
Usage | Polishing |
Specific Gravity | 2.6-2.8 |
Refractoriness | 1790°C |
Color | White |
Hardness | 7.5-8.5 |
Maximum Operating Temperature | 1700°F |
Service life | Long |
Mohs hardness | 7.5 |
Chemical Composition | Al2O3 |
Applications | Industrial Ceramic Parts, Industrial Ceramic Components, Silicon Carbide Ceramic Parts, Alumina Ceramic Parts |
Applications:
High strength and wear resistance
The main component of ceramic shot is zirconia, which is characterized by small crystal size and high wear resistance. Ceramic shot has high hardness, with Vickers hardness (microhardness) of 700hv and Rockwell hardness of 600hrc. The density and specific gravity are also much higher than those of glass beads.
No Dust emission
No dust, high abrasion resistance and strength make it difficult for ceramic shot to be broken during sand blasting, so it is not easy to generate dust.
Surface blasting effect
Using ceramic shot sandblasting can achieve smooth satin surface brightness. Using ceramic shot of the same specification is 60-70% lower than that of glass bead sandblasting. It is applicable to various metals and nonmetals, such as titanium alloy, magnesium alloy, aluminum alloy, stainless steel, carbon steel, brass and alloy, acrylic, plastic and other materials. Ceramic shot will not react or oxidize with metal, and there is no metal residue, so it will not affect the color of the workpiece.
Suitable for dry blasting and wet blasting
It is suitable for dry blasting and wet blasting. The surface of ceramic shot is very smooth, and the wear of sand blasting equipment is very small. Ceramic shot has high sandblasting efficiency and long service life, and its recycling times can reach 25 times of glass beads. The roundness is high, and the proportion of abnormal balls and snowman balls adhered between the spheres is low.
Customization:
We provide custom services for Ceramic Blasting Media. Our product features Fine-tech brand name, z210 model number, ISO9001 certification, 500KG minimum order quantity, negotation price, 25kg/barrel,25kg/bag,1t/pallet packaging details, 5-15work days delivery time, L/C,T/T payment terms, 2000t per year supply ability, Alumina Oxide abrasive grain, Polishing usage, Ceramic material, 7.5-8.5 hardness and low equipment wear. Our Ceramic Blasting Media are excellent for silicon carbide ceramic parts, industrial ceramic parts and industrial ceramic components.
Support and Services:
At Ceramic Blasting Media, we take pride in offering top-notch technical support and service to our customers. Our team of professional and knowledgeable technicians are available to answer any of your questions, provide helpful tips, and assist with product installation, maintenance, and troubleshooting.
We offer a variety of support options, including phone support, online chat, and email support. We also have a comprehensive help center with FAQs, troubleshooting guides, video tutorials, and more.
For additional assistance, our technicians are available 24/7 to answer your questions and help you with any issues you may have. We also offer a one-year warranty on all of our products to ensure that they are working properly.
If you have any questions or need help with our products, please don’t hesitate to contact us. Our friendly and knowledgeable team is here to provide you with the help you need.