High Hardness Zirconium Silicate Ball 125μm-250μm Spherical Dust Free
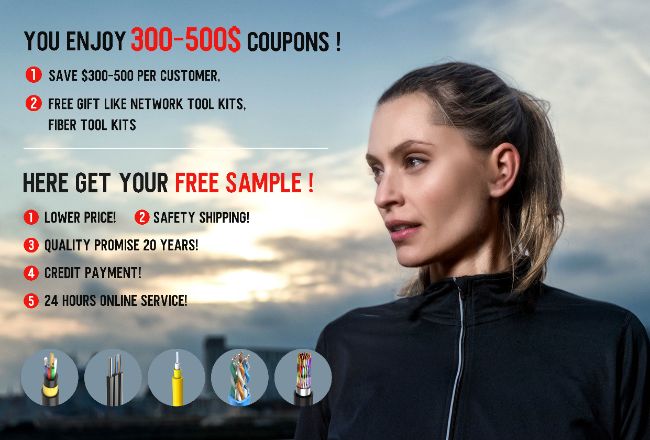
Contact me for free samples and coupons.
Whatsapp:0086 18588475571
Wechat: 0086 18588475571
Skype: sales10@aixton.com
If you have any concern, we provide 24-hour online help.
xFeatures | Spherical Dust Free | Shape | Ball |
---|---|---|---|
Size | 125-250 | SiO2 | 30%-35% |
Mohs Hardness | 7.5 | Survice Life | Long |
Highlight | High Hardness Zirconium Silicate Ball,Zirconium Silicate Ball 125μm |
Polishing B60 Zirconium Silicate Ball Uniform Surface Matting Effect
DESCRIPTION
Zirconium Silicate Ball B60 is zirconia-based blasting beads with high hardness and surface smoothness. As one recyclable sandblasting media, it is suitable for the blasting, finishing, cleaning, deburring, surface pretreatment in the process of metal parts production and maintenance.
Ziroconium Silicate Ball B60 is also called ceramic media, ceramic bead blasting media, or ceramic blasting beads.It is of high hardness, good elasticity, high gloss and high impact strength. Ceramic blasting beadsmainly used for blast cleaning, debluring, removing oxice layers of castings and forging parts, alsofor metal surface finishing, and pretreatment before coating and plating.
ADVANTAGES
1. High strength and wear resistance. The main component of ceramic shot is zirconia, which is characterized by small crystal size and high wear resistance.
2. Ceramic shot has high hardness, with Vickers hardness (microhardness) of 700HV and Rockwell hardness of 600HRC The density and specific gravity are also much higher than those of glass beads.
3. No dust, high abrasion resistance and strength make it difficult for ceramic shot to be broken during sand blasting, so it is not easy to generate dust.
4. Sandblasting effect: the surface finish is high. Using ceramic shot sandblasting can achieve smooth satin surface brightness. Using ceramic shot of the same specification is 60-70% lower than that of glass bead sandblasting.
APPLICATION
Zirconium Silicate Ball B60 can produce a uniform and uneven rough surface on the cleaned surface to facilitate mechanical bonding of the coating. Using clean compressed air to drive clean ceramic sand to spray on the surface of the workpiece can generate compressive stress on the surface of the substrate, remove the surface oxide film, and cause lattice distortion of part of the surface metal, which is conducive to the physical bonding of the coating. The substrate metal can be sandblasted to obtain a clean, rough and highly reactive surface. This is an important preprocessing method.
Shot peening of aviation parts: used to improve the fatigue resistance of carbon steel, titanium alloy, aluminum alloy and other
aviation mechanical parts and eliminate surface stress. It can be used for surface strengthening of aircraft wings, aeroengine turbine blades, turbine discs, gears and landing gear.