White Ceramic Blasting Abrasive 70μm - 125μm B120 Long Service Life
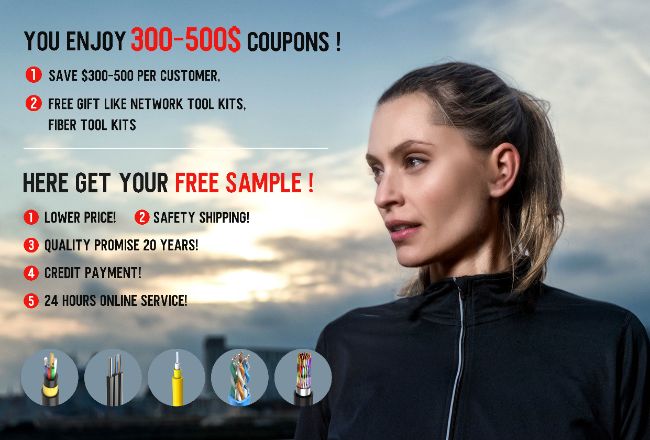
Contact me for free samples and coupons.
Whatsapp:0086 18588475571
Wechat: 0086 18588475571
Skype: sales10@aixton.com
If you have any concern, we provide 24-hour online help.
xName | Zirconia Ceramic Beads | Material | Zirconia |
---|---|---|---|
Production Technology | Melting Method | Color | White |
Chemical Composition | ZrO2 65% SiO2 35% | Type | B120 |
Place Of Origin | Changsha, China | ||
Highlight | White Ceramic Blasting Abrasive,Ceramic Blasting Abrasive 70μm,Ceramic Blast Media 125μm |
White 70-125μm Ceramic Blasting Abrasive B120 Long Service Life
INTRODUCTION
Ceramic blasting abrasive is made by using unique technological formula, special production technology and high temperature fixed phase synthesis method above 2000℃. The ceramic sand can generate a gentle grinding effect, resulting in a uniform surface profile and matte finish, which is durable and efficient without inlaying contamination to the metal body. Low dust content, high degree of sphericity, smooth spherical and high toughness ensure excellent performance of ceramic sand products. They are suitable for sandblasting the surfaces of various steel, aluminum and other non-ferrous metal alloys to remove oxides, rust, sand, coatings and burrs. It can clean molds, engine parts, turbomachinery parts, welded steel parts, forged and cast metals and other various industrial components. Providing high quality components with outstanding aesthetic appearance in a variety of applications such as automotive, aerospace, electronics, home appliances, sporting goods and construction to achieve outstanding smooth and even surface finish on the parts being treated.
ADVANTAGES
· It is applicable to various metals and nonmetals, such as titanium alloy, magnesium alloy, aluminum alloy, stainless steel, carbon steel, brass and alloy, acrylic, plastic and other materials. Ceramic shot will not react or oxidize with metal, and there is no metal residue, so it will not affect the color of the workpiece.
· Ceramic blasting abrasive has high hardness, with Vickers hardness (microhardness) of 700HV and Rockwell hardness of 600HRC The density and specific gravity are also much higher than those of glass beads.
· Ceramic blasting abrasive has high sandblasting efficiency and long service life, and its recycling times can reach 25 times of glass beads.
· High strength and wear resistance. The main component of ceramic shot is zirconia, which is characterized by small crystal size and high wear resistance.
APPLICATION
1. Medical treatment: surface treatment such as deburring of stainless steel surgical instruments and titanium alloy human implanted devices.
2. High iron field: it can be used for sandblasting the surface of high iron aluminum alloy parts to improve the metal texture and form a smooth satin effect. Used for grinding and finishing of high-speed rail.
3. Automotive field: ceramic shot can be used for surface cleaning and deburring of Automotive Engine Castings; It is used to clean the welds and welding spots on the car floor and prepare for subsequent spraying; Used for shot peening of automobile springs to improve fatigue life. It is used for beautification and sandblasting of aluminum alloy automobile wheels to eliminate stress and improve impact resistance.
FEATURES
· White color, high sphericity and smooth surface beads.
· Utilization rate(20 – 30 times) higher than glass blasting media.
· High hardness, unbreakable, can be recycled and used repeatedly, long service life, reduce energy consumption and reduce costs.
· Lower metal surface roughness.
· Less operation pressure and reduced abrasive velocity needed than glass blasting media, thus have far less abrasive breakdown and dust generation, results in cleaner working environment and better operator visibility.
· Strong mechanical resistance and high toughness, but gentle with equipment and tools preserving work parts, and no metallic contamination for treated parts.